métallurgie - physique.
Publié le 24/04/2013
Extrait du document
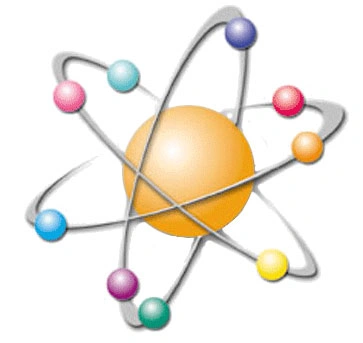
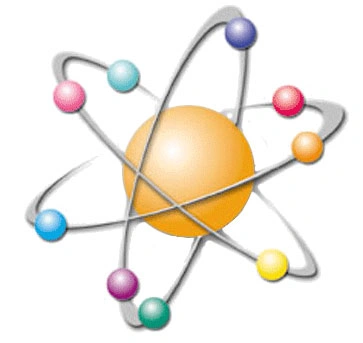
«
La production en tonnage de métal séparé et purifié par fusion est plus importante que par tout autre procédé.
Le minerai, préalablement dissocié par un procédé de séparation mécanique, est ensuite porté à haute température en présence d’un agent réducteur ( voir Oxydoréduction) et d’un flux (produit déposé à la surface du bain de fusion).
L’agent réducteur se combine à l’oxygène pour donner un oxyde métallique, alors que le flux s’associe à la gangue pour former une scorie liquide qui peut êtreécumée et séparée du métal.
La production de fonte brute dans les hauts-fourneaux en est un exemple ( voir Sidérurgie).
De même, ce procédé est également utilisé dans la purification du cuivre, du plomb, du nickel et de nombreux autres métaux.
Plus onéreuse, la réduction directe de l’oxyde métallique par l’hydrogène est adaptée à des métaux tels que le molybdène et le tungstène (elle permet d’obtenir des produitstrès purs, et aussi d’éviter les carbures métalliques que le coke produit).
Voir aussi Ellingham, diagramme d’.
5.2 Électrolyse
On procède par électrolyse pour l’aluminium ou le sodium — tous deux très électronégatifs — ( voir Électrochimie).
Elle est réalisée dans une solution aqueuse ou dans un four à électrolyse.
Le cuivre, le nickel, le zinc, l’argent et l’or sont des exemples de métaux raffinés par sédimentation dans des solutions aqueuses.
L’aluminium, le baryum,le calcium, le magnésium, le béryllium, le potassium et le sodium sont des métaux qui sont raffinés dans des fours à électrolyse.
Par exemple, pour l’aluminium, on faitfondre l’alumine (Al 2O3) dans un bain de cryolite (Na 3AlF6), à 960 °C.
L’alumine se décompose alors par électrolyse à faible tension (4 V) : l’oxygène est attiré vers l’anode en carbone et produit du gaz carbonique, alors que l’aluminium est recueilli sur la cathode placée au fond du creuset.
On utilise aussi l’aluminium pour réduire l’oxyde dechrome (Cr 2O3).
La pureté de ce dernier dépend de la pureté de l’aluminium employé.
Les deux substances sont introduites dans le creuset.
Un ruban de magnésium y est enflammé ; la chaleur produite permet d’entretenir la réaction, jusqu’à ce qu’au fond du creuset se constituent deux couches de produits, l’une constituée de chrome pur,l’autre, d’un mélange d’alumine et d’oxyde de chrome, que l’on peut, une fois refroidies, séparer facilement.
5.3 Fusion de zone
Le silicium est d’une grande importance pour l’industrie des semi-conducteurs, qui a pris un essor considérable durant ces dernières décennies.
L’industrie informatique enfait un très large usage.
Elle exige un silicium présentant un degré de pureté très élevé (à 99,999 p.
100), que l’on obtient par le procédé de fusion de zone, les méthodesde purification chimique conduisant à une pureté nettement inférieure.
Après purification chimique, on chauffe juste au-dessus de la température de fusion, par induction decourants hyperfréquence ou par bombardement électronique, une petite zone à une extrémité d’une barre de silicium.
Dans cette zone désormais liquide se rassemblentalors les impuretés limitrophes.
Petit à petit, on déplace la zone de silicium en fusion vers l’autre extrémité de la barre, et on revient de la même manière, jusqu’àrassembler l’ensemble des impuretés dans la même zone, que l’on supprime ensuite.
Voir aussi Semi-conducteur.
5.4 Enrichissement de l’uranium naturel
L’uranium naturel contient 99,3 p.
100 de l’isotope 238, lequel n’est pas fissile, et 0,7 p.
100 de l’isotope 235, fissile.
Afin qu’il serve de combustible pour les centralesnucléaires, l’isotope 235 doit être présent à un pourcentage compris entre 2 et 4 p.
100 : c’est ce que l’on appelle l’uranium enrichi.
Pour obtenir ce dernier, on combine del’uranium naturel à du fluor, afin d’obtenir un gaz, l’hexafluorure d’uranium.
Puis on contraint ce gaz à traverser plusieurs milliers de fois des barrières poreuses.
Commel’isotope 235 les traverse légèrement plus vite, l’uranium recueilli a une teneur en cet isotope supérieure à celle de l’uranium de départ.
Un autre procédé, qui n’est toutefoispas encore opérationnel à échelle industrielle, consiste à séparer les deux isotopes par laser (photo-ionisation sélective).
Voir aussi Matériaux, science et technologie des ; Métallographie ; Métaux ; Sidérurgie.
Microsoft ® Encarta ® 2009. © 1993-2008 Microsoft Corporation.
Tous droits réservés..
»
↓↓↓ APERÇU DU DOCUMENT ↓↓↓
Liens utiles
- poudres, métallurgie des - physique.
- fonte (métallurgie) - physique.
- Oral physique-chimie/maths: l'heure du crime !
- Niels Bohr: Physique atomique et Connaissance humaine
- devoir laboratoire physique chaleur massique